Common Welding Defects and How You Can Identify Them
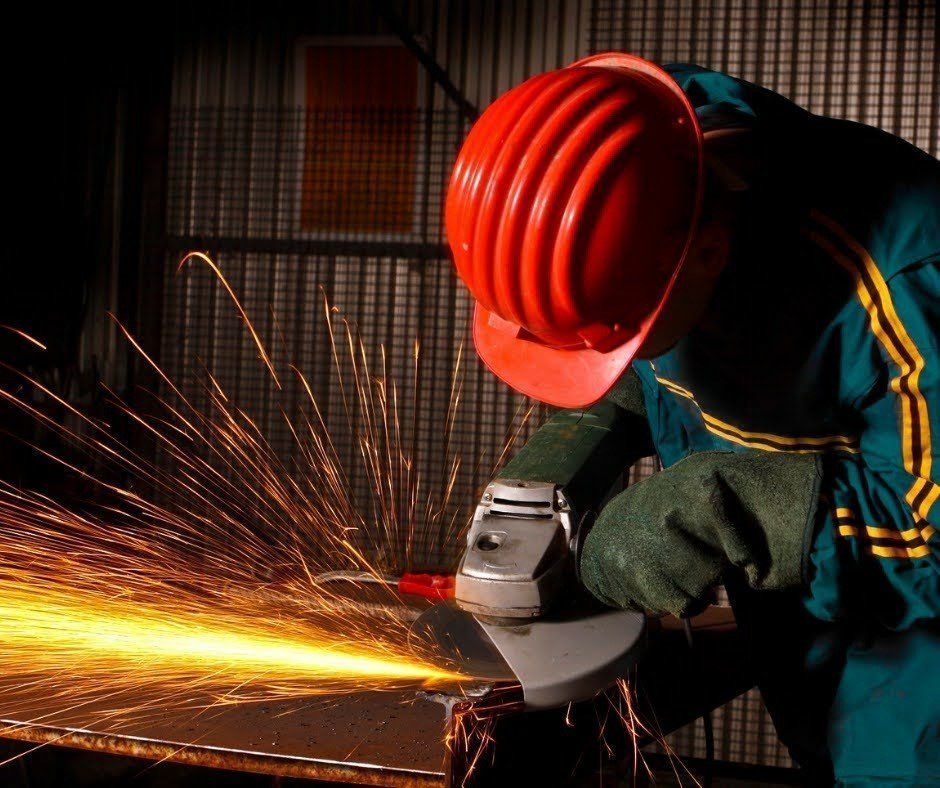
Defects are common in welding projects, as is the case with many other fabrication jobs. A welding defect can alter the appearance of a finish, causing variations in both size and shape of your project.
Under intense heat, metal acts differently from other materials. For instance, heat causes metal to expand during welding, which in turn weakens its grain structure. After cooling, the brittle metal can easily break or develop cracks that will only get worse with time.
Having an experienced professional take on your welding projects is an excellent way to ensure quality welding built to last longer. But before you hire an expert, you should be able to identify different welding defects as you keep tabs on your project. Here are the most common defects and how you can easily catch them.
Porosity
Porosity happens when oxygen, nitrogen, and other gas bubbles remain enclosed by the weld pool. The welding defect leaves behind distracting bumps on the weld after solidifying on the weld surface.
However, porosity can also occur under the weld surface and can be difficult to see with your naked eye. A welding professional often uses X-ray technology to determine whether the weld has any porosity. Some reasons behind the defect include:
- Contaminants such as dirt, oil, and rust trapped in the weld
- Trapped gasses in the molten weld before solidification
- An improper welding technique
- Insufficient coating on the electrode
A qualified welding expert will have the necessary knowledge to choose a technique with minimal chances of porosity. They'll be sure to prepare the weld surface and get rid of any oil or rust that might cause defects in the final finish.
Undercutting
Undercutting has a massive impact on a weld's quality and could cost you more money to correct. Typically, this welding defect appears as a groove and sits at the base of the weld. The weld metal then fails to completely cover the groove section resulting in a weak weld.
Soon, cracks develop around the toe of the weld, further diminishing the integrity of the finish. They could occur when:
- The plate thickness is too small for the electrode
- The arc voltage exceeds maximum limits
- The travel speed is higher than required
- The electrode angle is wrong
Preventing undercuts saves money and time during your welding project. A skilled welding professional is adept at manipulating welding equipment at the right speed to avoid such problems.
Weld Cracks
Weld cracks are considered to be a severe welding defect by industry standards. Cracks can sometimes be difficult to predict or identify since they can occur at different temperatures.
They appear as a discontinuity between the filler and base metals. Cracks could result from quick cooling, contamination, and internal stresses between the base and weld metal. Weld cracks typically appear in the following three forms:
- Hot cracks. They often appear inside the weld material immediately after completing the welding process. Poor design or Sulphur presence in the base metal could result in hot cracks.
- Cold cracks. These cracks take longer to appear, typically a day or so after welding. Cold cracks are caused by hydrogen leaks into the weld puddle and are more common with steel welding.
A professional welding contractor avoids cracks by getting the fit-up right to align correctly with the base metal. They also check their equipment to ensure that heat is enough to preheat the metal to the desired level, free of leaking hydrogen.
Although welding jobs are fairly straightforward, issues from mistakes and defects are relatively common. But with the right help, you can be sure of a clean and reliable weld to serve you for years to come. For more welding insights, reach out to
Spradlin Bros. Welding Co. today.